1. What's the Secret to Tapered Roller Bearing?
ORS Bearings has contributed to this improvement by producing 9 different types of bearings. ORSKOREA manufactures and supplies the grinding machines necessary for bearing production of ORS Bearings.
Then what types of bearings have shaped human history, and how are they made?
In this blog series, we will explore how Tapered Roller Bearings (a type of Roller Bearings) are made by the grinding process.
First of all, we’ll focus on what ‘Tapered Roller Bearings’ are, and the key grinding methods used in their production.
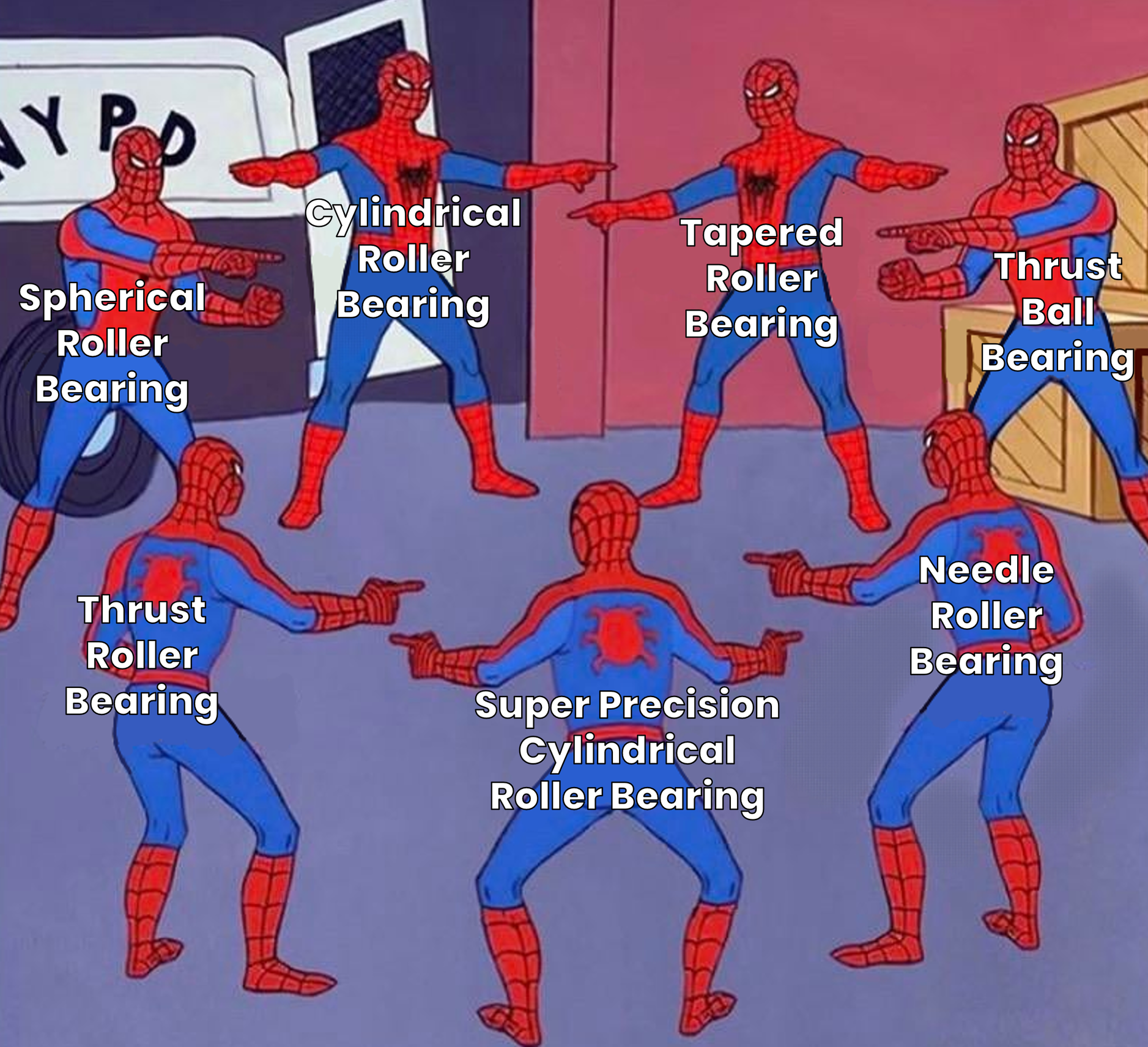
Tapered Roller Bearings
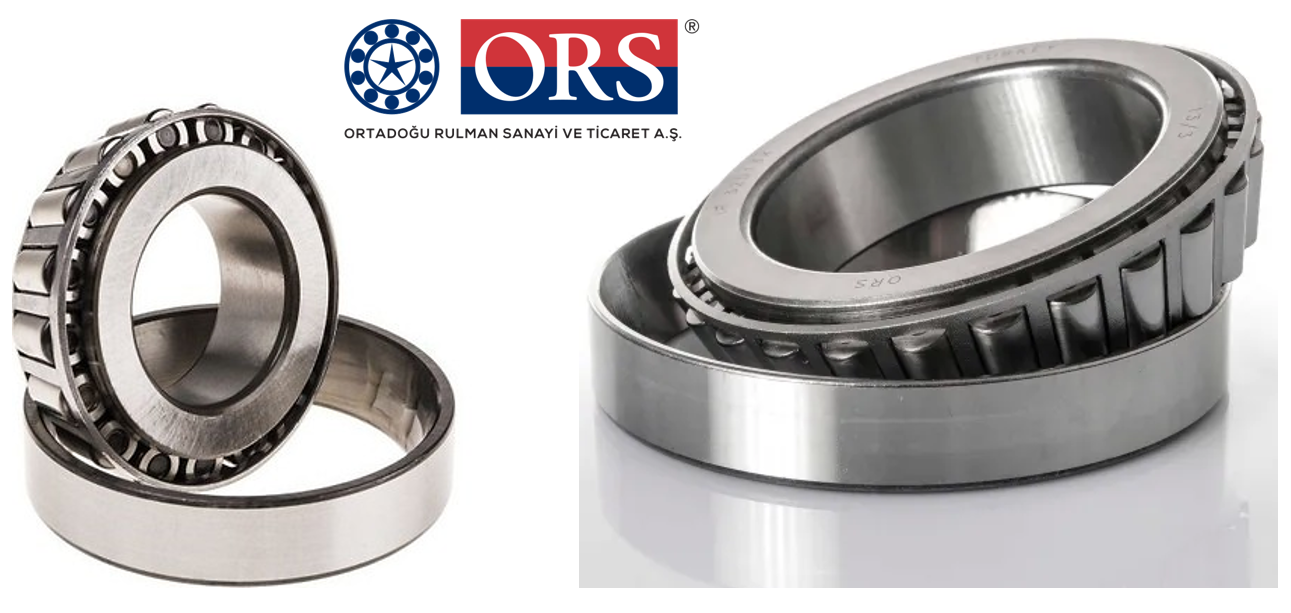
Tapered roller bearings(TRBs) are designed so that the imagined conical apices formed by the raceways of the inner and outer rings and the rollers all converge at one point on the bearing axis.
TRBs can take radial loads and axial loads in one direction.
When load is applied, the axial component generated inside the bearing generally requires the use of two opposed bearings (similar to angular contact ball bearings) or double-row bearings.
Spacers are used to adjust the inner and outer rings in the axial direction to achieve the proper internal clearance. Since they are separable, the inner ring (cone) assemblies and outer rings (cups) can be mounted independently.
[Ref. NSK]
ORS Bearing also produces tapered roller bearings, ORSKOREA provides grinding machines to produce high-quality bearings.