Tapered Roller Large End Face Grinding
⚙️
How can we manufacture high-quality tapered roller bearings?
As shown in the picture below, we can achieve a smooth surface on even hard materials through large end face grinding.
In a previous post, we learned about centerless grinding and maintaining the importance of consistent centerline.
This time, we'll explore how to produce top-notch bearings through a fast and efficient process.
Let's dive into the key factors that must be considered to deliver the quality that consumers demand!
As shown in the picture below, we can achieve a smooth surface on even hard materials through large end face grinding.
In a previous post, we learned about centerless grinding and maintaining the importance of consistent centerline.
This time, we'll explore how to produce top-notch bearings through a fast and efficient process.
Let's dive into the key factors that must be considered to deliver the quality that consumers demand!
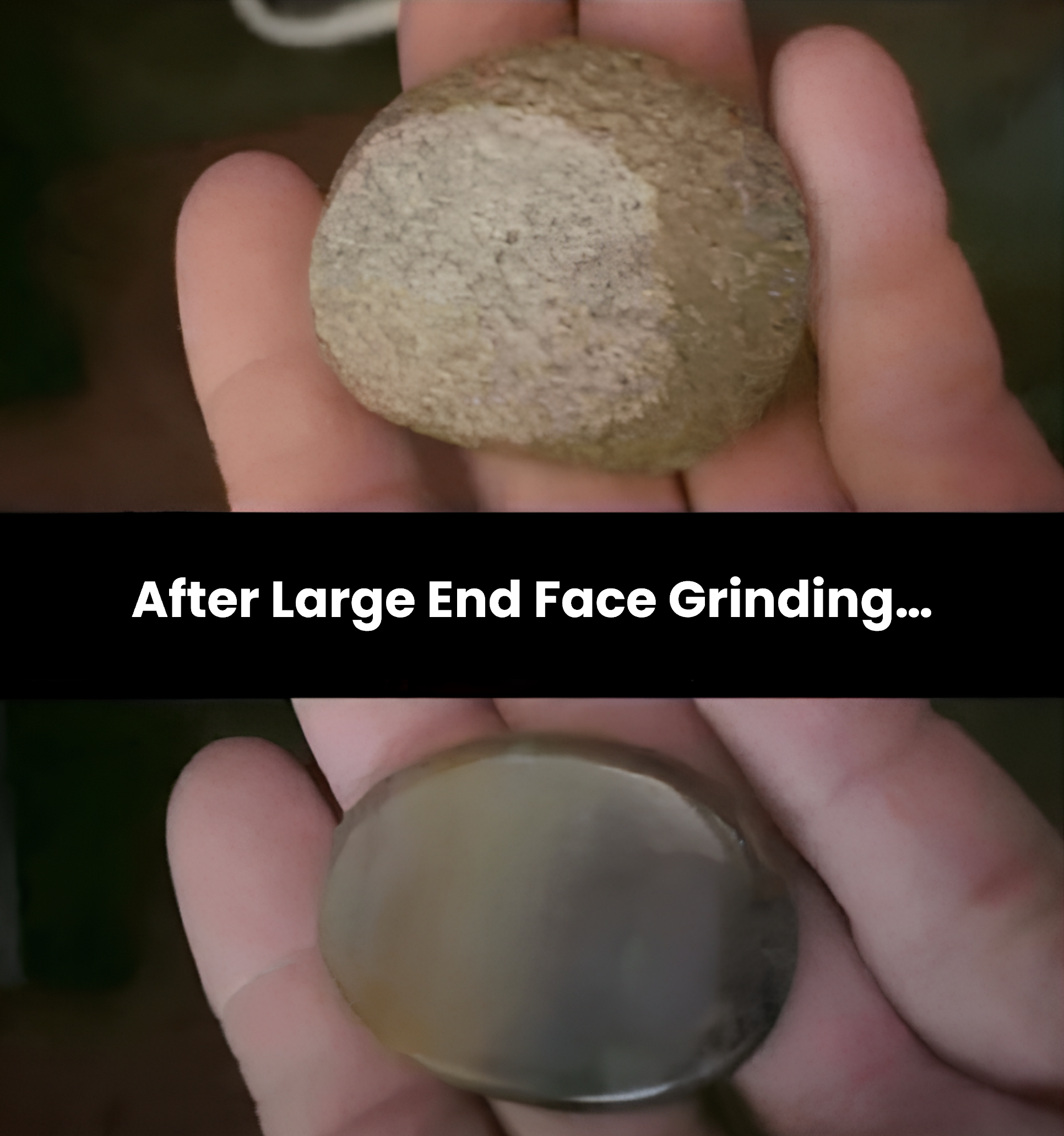
Tapered roller large end face grinding
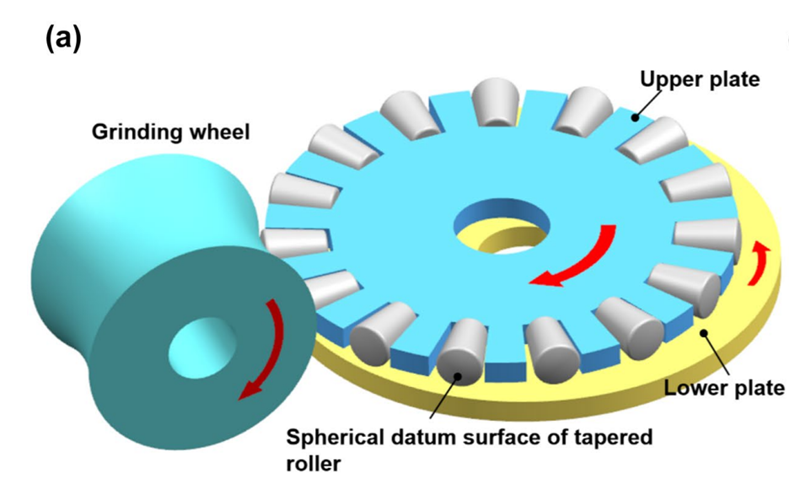
The tapered rollers are guided by sliding contact between the tapered roller large end face and the inner ring large rib face within a tapered roller bearing.
Therefore, the large end face of the tapered rollers must achieve a very fine surface finish and exact geometry.
The undulation of the large end face determines the rotational stability of the tapered roller bearing, and the smaller the large end face runout, the greater the improvement in the rotational smoothness.